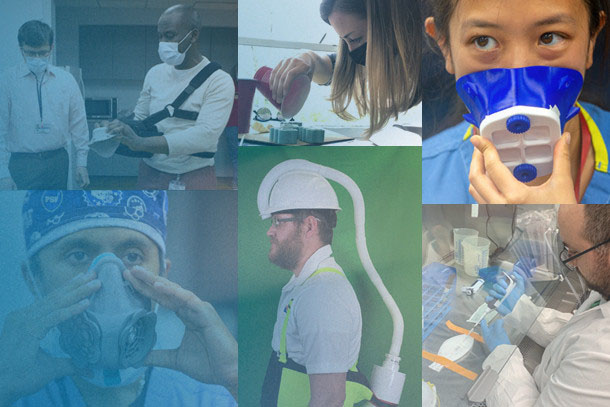
Over the past year, MASC researchers have designed, tested, manufactured and delivered hundreds of thousands of PPE to healthcare workers. IMAGE: MASC, PENN STATE HEALTH MILTON S. HERSHEY MEDICAL CENTER, JASON PLOTKIN
University-wide COVID-19 response initiative marks a year of solutions, impact
More than 350 researchers joined a coalition to rapidly design and deploy critical equipment to frontline health care workers
3/29/2021
By Erin Cassidy Hendrick
UNIVERSITY PARK, Pa. — One year ago, as physicians and administrators at Penn State Health’s Milton S. Hershey Medical Center prepared for the impact of COVID-19, a consortium of Penn State researchers joined together to make a positive impact.
In March 2020, that effort launched the Manufacturing and Sterilization to address COVID-19 (MASC) Initiative and quickly expanded to include more than 350 researchers, faculty, staff and health care professionals spanning the entire University, including the College of Engineering, College of Medicine, Materials Research Institute (MRI), Applied Research Laboratory (ARL) and Smeal College of Business.
“We knew that this challenge was way too big for any one lab to handle alone,” said Tim Simpson, founder of MASC, interim department head of the School of Engineering Design, Technology, and Professional Programs (SEDTAPP) and the Paul Morrow Professor in Engineering Design and Manufacturing. “We pulled together engineers, physicians, scientists, artists, supply chain experts, administrators and even alumni to mobilize the power of Penn State to protect our health care providers and communities across the commonwealth.”
Beginning as an ARL-led project to 3D-print face shields, word spread about the initiative and soon researchers, faculty, staff and students began rapidly designing and delivering a wide range of products for the University, its health system and broader community.
Teams were quickly formed by connecting researchers with a wide array of expertise. Forged by these interdisciplinary strengths, the University’s 3D-printing capabilities and other prototyping technologies, the resulting projects were accelerated.
“For example, a team led by Jessica Menold was able to complete the first prototype of a 3D-printed disposable stethoscope within a single weekend,” Simpson said.
Menold, the Hartz Family Career Development Assistant Professor of Engineering Design and Mechanical Engineering, and her team delivered dozens of prototypes to the Hershey Medical Center for rapid feedback from clinicians to improve design and acoustic quality.
Barry Fell, a consultant for the Department of Surgery at the Hershey Medical Center and MASC team member, worked with Menold to finalize a manufacturable design, enabling mass-production at a local Good Manufacturing Practice (GMP) facility, regulated by the federal government, to address the urgent need.
In addition, MASC, partnering with local GMP manufacturers, has designed, fabricated and delivered hundreds of thousands of pieces of personal protective equipment (PPE) such as face shields, masks and gowns over the past year.
“The MASC initiative assembled the tremendous expertise and interdisciplinary resources we have at Penn State to develop rapid solutions that could support our health care system and our communities during the pandemic,” said Erika Swift, associate director of the Center for Medical Innovation at Penn State. “MASC also ensured compliance with regulatory agencies, such as the FDA’s Emergency Use Authorizations, by creating a quality control system and partnering with local GMP manufacturers.”
In addition to leveraging the strength of the University’s expansive research enterprise across the commonwealth, MASC teamed with several industry partners, including Universal Protective Packaging Inc. (UPPI), Hershey Company, 3D Systems, 3M, Actuated Medical, and Plastikos Inc., to help source materials, manufacture and assemble PPE to meet regulatory requirements.
UPPI, which manufactures medical packaging in Mechanicsburg, was one of MASC’s first industry partners. They were able to pivot their assembly lines to produce over 720,000 face shields for Penn State Health and surrounding health care providers. In addition to supplying much-needed PPE, this production was also critically important to UPPI, since their business relied heavily on elective surgeries that were halted due to the pandemic.
“Face shield manufacturing and assembly provided a way for us to keep many people employed at the beginning of the pandemic shutdowns,” said Tim Ritter, vice president at UPPI.
After responding to these critical, time-sensitive needs, MASC began to transition from a rapid design and deployment response team to an advanced research and development initiative, led by the Penn State Center for Biodevices.
Showcasing the group’s multidisciplinary reach, the initiative is now co-directed by Swift, Mary Frecker, professor of mechanical engineering and biomedical engineering and the director of the Center for Biodevices, and Michael Hickner, associate director of MRI and professor of materials science and engineering and chemical engineering.
“The lessons learned through the pandemic response will be carried forward as we shift our sights to instilling pandemic readiness,” Swift said.
To that end, the teams continue to develop new solutions and inventions, emerging from the partnerships developed over the past year between University Park researchers and physicians at Penn State Health.
“Reflecting on what MASC has accomplished over the past year, it is clear that Penn State researchers rose to the challenge presented by the pandemic,” said Lora Weiss, senior vice president for research. “MASC is an example of how the University has the capacity, creativity, empathy and wherewithal to rapidly pivot during a crisis and specifically to make an impact in helping our front-line health care workers.”