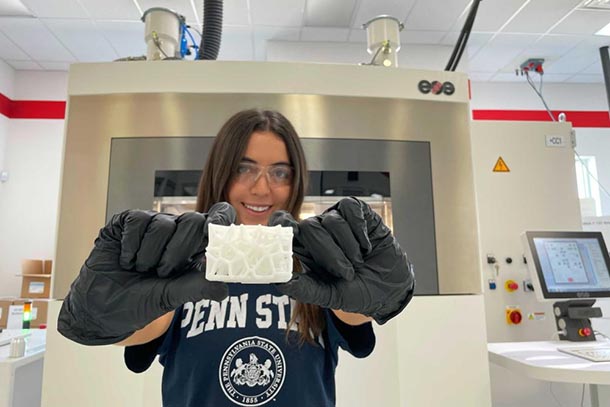
Paula Clares with a 3D printed lattice structure at EOS, where she completed an internship. IMAGE: PROVIDED
3D-printing grad student helps optimize emerging technology
10/28/2021
By Erin Cassidy Hendrick
UNIVERSITY PARK, Pa. — With several research advancements and an industry internship under her belt, Penn State graduate student Paula Clares feels prepared to make a sizable impact in the 3D-printing industry.
With projects ranging from 3D-printing ceramics to polymers to metals, she explained earning her master’s from the Additive Manufacturing and Design Program is setting her up for success.
“It covers everything someone would need: design, theory and electives you can choose based on your interests,” said Clares, who will be graduating in the spring. “Even after one year, I felt the program is preparing me 100% for the industry.”
With multiple material options, Clares said, 3D-printing technology creates unique components layer by layer, unlocking a previously unimagined design freedom and complexity.
As a graduate researcher in the SHAPE Lab - Systems for Hybrid-Additive Process Engineering Lab, Clares explores how a mixture of particle sizes within the materials could potentially strengthen and enhance a component’s use and applications.
“I was hypothesizing that if you use a mixture of different-sized particles, called bimodal size distribution, for 3D-printing ceramic, you can achieve higher density, flowability and lower porosity,” she said. “By increasing these mechanical properties, at the end of the day you will have a stronger part.”
She presented her results at Manufacturing Science and Engineering Conference (MSEC 2021), which is organized by ASME, the American Society of Mechanical Engineers.
Clares explained that ceramics are an interesting material to study since their distinct characteristics, including high hardness, resistance to wear and bio-capabilities, make them attractive for many 3D-printed applications in aerospace, biomedical and automotive industries.
However, she isn’t limiting herself to one material.
EOS, an industrial 3D-printing company specializing in metal and polymers based near Austin, Texas, hired Clares as an intern within their Additive Minds team this past summer. Through this experience, she extended her expertise to polymer lattice structures, which are honeycomb-like designs, as opposed to completely solid pieces, that can add unique and useful properties to 3D-printed components.
“Lattice structures have a good weight-to-strength ratio and they’re great for shock absorption and impact,” she said. “For example, you can design a football helmet with a lattice structure that could absorb a hit better than a solid piece, since each structure will dampen the hit before it reaches the person.”
But to create a cutting-edge product like this, different polymer materials, designs and variables of the lattice structure need to be fully explored and defined. Leveraging the company’s Digital Foam technology under the guidance of EOS’ David Krzeminski, Clares designed experiments and conducted testing for a project intended to become the “guidebook” for 3D-printing these pieces.
“There are so many different parameters you can adjust, such as cell size, lattice type, how thick they are,” she said. “All of these combinations can produce different performance and use. The main goal for my project was to collect and test the data from different lattice structures and build a database that can be a reference for additive manufacturing designers.”
So, theoretically, an engineer 3D-printing a new type of football helmet could discover which exact type of lattice structure fits their needs, without conducting their own experimentation.
“That complex, fundamental work is already done for them with this database,” Clares said.
Clares’ research has been accepted for presentation at a 2022 International Sports Engineering Conference.
With the knowledge gained from her internship and her 2020 work in the SHAPE Lab, guided by Guha Manogharan, the Emmert H. Bashore Faculty Development Assistant Professor, she set out to see whether the effects of bimodal size distribution could also enhance metal-based 3D-printed parts.
This semester, she is performing computational and experimental work to help optimize the metal 3D-printing process for stronger mechanical properties.
“I wanted to explore if the responses I was getting in ceramics with bimodal size distribution applied to metals,” Clares said. “It’s about expanding the scope of this knowledge and seeing what is possible.”
As a relatively new frontier in manufacturing, she explained that research in 3D printing, including her own, has the potential to influence the future of the industry and the technology’s applications.
“Every discovery can have a huge impact,” she said. “It’s such an up-and-coming technology, every discovery opens the door for people to further investigate and build.”