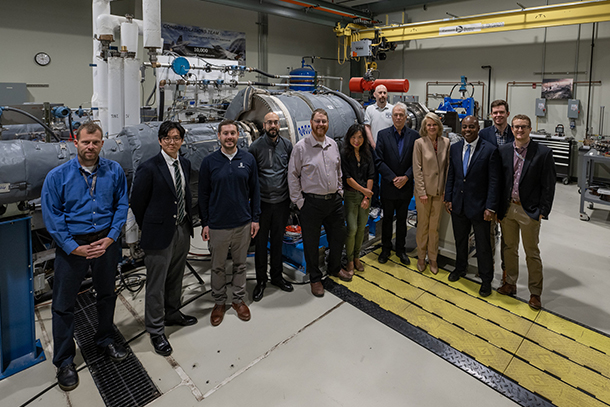
Representatives from Pratt & Whitney, the Federal Aviation Administration, the U.S. Department of Energy and Penn State met in the START Lab at Penn State in October 2022. Together, these groups have committed nearly $26 million to a two-part expansion of the lab to further research for sustainable aviation. Photo credit: Kelby Hochreither/Penn State
$26M START Lab expansion to advance sustainable power and propulsion
March 15, 2023
By Sarah Small
UNIVERSITY PARK, Pa. — To create new solutions for sustainable power and propulsion research through advancing gas turbine technologies, Pratt & Whitney, the Federal Aviation Administration (FAA), the U.S. Department of Energy National Energy Technology Lab (DOE-NETL) and Penn State have joined together to support our nation’s needs. The resulting project involves a $26 million commitment to support the Steady Thermal Aero Research Turbine (START) Lab in both expanding the existing capabilities, as well as adding a new, two-stage turbine rig referred to as START+ at University Park. The FAA’s initial $1.1 million grant under the Aviation Sustainability Center of Excellence (ASCENT) is the beginning of a five-year effort that will focus on development of the new START+ two-stage turbine rig, while DOE’s award of $4.5 million will focus on expansion of overall START rig capabilities via new air compressors.
Led by Penn State Distinguished Professor of Mechanical Engineering Karen Thole, the START Lab was founded in 2012 in the Penn State Department of Mechanical Engineering through a partnership with the DOE-NETL and Pratt & Whitney. The turbine testing facility was designed to perform turbine heat transfer studies, along with instrumentation development and integration of additive manufacturing to increase the speed in advancing turbine research. The START facility has not only tested proprietary turbine blades and vanes but, through the support and work by DOE-NETL and industry, the START team has also developed the National Experimental Turbine (NExT). Industry partners who supported and guided the design of NExT include Honeywell, Pratt & Whitney, Siemens Energy and Solar Turbines, with the design details by Agilis.
The START expansion, expected to begin in spring 2023 and conclude in five years, includes adding four compressors to the two existing compressors — these are the components that provide high-pressure air to the test turbine. These new compressors will increase the flow and pressures needed to evaluate turbine vanes manufactured from new high-temperature materials and also to simulate relevant combustor profiles that result from the use of different fuels, such as lower aromatic content sustainable aviation fuels and zero-carbon fuels such as hydrogen or ammonia, coming into the turbine.
The other addition is START+, a completely new two-stage test turbine designed to help researchers understand impacts of shrinking the turbine core. Two-stage turbines are an increasingly prominent design in new engines and can enable greater efficiency and reduced emissions. According to Scott Fishbone, research engineer in the START Lab who will oversee the expansion, this will help the team develop a new generation of more efficient turbine engines for aviation. This includes turbines relevant to future hybrid electric propulsion concepts for aviation.
“This is a major upgrade to our testing capabilities and one that our industry partners are excited to have,” Fishbone said.
Michael Barringer, associate research professor in the START Lab, explained further.
“The expansions to the START Lab provide the needed capabilities to increase turbine thermodynamic efficiency, which in turn contributes to reducing the engine carbon dioxide (CO2) emissions, leading us towards sustainable aviation and power generation,” Barringer said.
According to Thole, those are the two main applications for which gas turbines are critical: aviation — propelling planes through the sky — and generating electricity.
Air travel accounts for nearly 2.5% of all CO2 emitted from fossil fuel use, with roughly 90% of that coming from large commercial jets. Thole explained there are four major possible propulsion-related solutions to reduce these emissions for aviation.
“One solution is to use sustainable aviation fuels,” she said. “Many are also looking at using hydrogen as a fuel for aviation; and a third solution is to create a hybrid electric propulsion system, much like flying a Toyota Prius in the sky. Yet a fourth solution to reduce CO2 emissions of aviation is to go fully electric with batteries. Fully electric for large aircrafts is not feasible — and won’t be in my lifetime — because the battery requirements for getting a plane off the ground have significant energy density needs. So, it comes down to three of the four solutions all involving efficient turbines.”
Thole said that increasing turbine efficiency makes a big difference in CO2 emissions for turbines used in power generation as well.
“While there are other solutions for reducing emissions from power generation, many come at a high price,” Thole said. “However, increasing turbine efficiency by one point is equivalent to taking off two million cars from the road in terms of the CO2 impact.”
In addition to increasing turbine efficiency and extending airfoil — vane and blade — life, the START Lab develops unique instrumentation and measurement methods capitalizing on additive manufacturing, according to Reid Berdanier, associate research professor in the START Lab.
“Turbines have stationary vanes and spinning blades, and our research team has developed an infrared thermal imaging probe that captures temperatures of blades spinning at 10,000 revolutions per minute — which is equivalent to 500 miles per hour,” Berdanier said.
According to Berdanier, the temperature measurements are important for assessing new cooling methods that can also increase efficiency and extend the life of the blades.
“The goal is to operate a turbine at the highest possible temperature, because elevated temperatures lead to high efficiencies, but this comes at an expense of reducing blade life for the same cooling flow,” Thole said. “With the capabilities to measure blade temperatures, we can advance new geometries and new manufacturing methods for cooling airfoils. Being able to use an infrared camera to map the temperature onto the blades — which is a unique capability developed in the START Lab — saves the turbine manufacturers money and time because we can get meaningful data that maps directly to performance in an engine.”