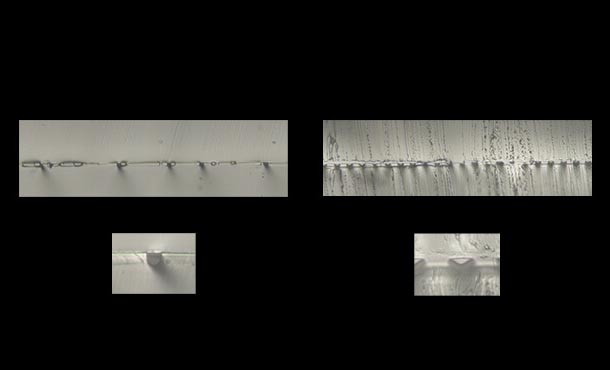
Researchers found that treating the same material at different stages of preparation could produce controllable valves for microfluidic devices. On the left, the material was stretched after treatment, resulting in cracks. On the right, the material was stretched before treatment and released, producing wrinkles. The bottom images are close ups of a crack and a wrinkle, respectively. IMAGE: HUANYU “LARRY” CHENG/PENN STATE
Intentional cracks and wrinkles provide low-cost option for medical screening
7/30/2021
By Ashley J. WennersHerron
UNIVERSITY PARK, Pa. — Size matters when it comes to sorting biological materials. From identifying pathogens to screening for drug treatments, the ability to quickly identify and separate particles based on their size is an increasingly important tool in diagnosing and treating patients, according to Huanyu “Larry” Cheng, Dorothy Quiggle Career Development Professor in Penn State's Department of Engineering Science and Mechanics. Cheng and his international collaborators at Xiangtan University in China developed a low-cost, efficient way to fabricate a flexible sorting device for use in biomedical sensors.
They published their approach this week in ACS Applied Materials & Interfaces, a journal of the American Chemical Society.
Traditional microfluidic devices are produced with precise measurements to sort specific sized particles, such as identifying the pathogens underlying an infection in a patient’s blood. The devices are built in clean rooms with highly specialized equipment to achieve the necessary degree of accuracy.
“Microfluidic devices are very important, but we need to do a better job fabricating them,” Cheng said. “Current methods can take days, if not weeks, and they are often expensive.”
To reduce the cost and time of producing the devices, the researchers took inspiration from what they want to monitor: the bendy, stretchy, sometimes wrinkly human body.
They used a polymer containing carbon and silicon called PDMS, which becomes stiff when treated with ultraviolet light. Once the top surface of the polymer was stiff, they stretched it out, creating tiny cracks in the stiff layer. The researchers then encapsulated it with another cap layer of the same polymer.
Next, they repeated the process but stretched the polymer before treating it with UV light. Once they released the stretched polymer with a stiff surface, it crinkled, with little wrinkles lining its face.
When the devices are stretched and released, the cracks and wrinkles operate as valves, allowing small particles to flow through while restraining larger objects.
“We can use the cracks or the wrinkles to manipulate the fluid flow,” Cheng said. “These mechanical deformations aren’t new, but they haven’t been explored for use in microfluidic devices. We ended up with a nice marriage between the two structures, which can be fabricated simply and at a low cost.”
Cheng focuses on developing flexible, stretchable sensors capable of wirelessly monitoring a person’s health through their physical motions and chemical signals in their sweat, skin and more. The goal, he said, is to improve the patient’s comfort and quality of life while obtaining as much information as possible to help inform diagnosis and treatment.
“We want to develop a standalone, stretchable system that allows for the long-term, continuous use of wireless sensing devices to advance both the capabilities and comfort of health monitoring for patients,” Cheng said. “The ability to manufacture a low-cost, large-scale approach to allow for further testing is a critical component of such a system.”
The researchers plan to continue collaborating, Cheng said, and will explore how to produce and use the microfluidic device even more efficiently.
Other contributors include Ying Liu, Min Cheng, Jielong Huang, Yangchengyi Liu, Yao Chen, Yang Xiao, Shangda Chen, Xiaoping OuYang and Xiufeng Wang, all of whom are affiliated with Xiangtan University.
The National Natural Science Foundation of China, the Natural Science Foundation of Hunan Province, the Scientific Research Fund of Hunan Provincial Education Department, the Open Fund from the Zhejiang Tsinghua Institute of Flexible Electronics Technology, the U.S. National Science Foundation, the American Chemical Society Petroleum Research Fund, the U.S. National Heart, Lung, and Blood Institute, and Penn State supported this work.