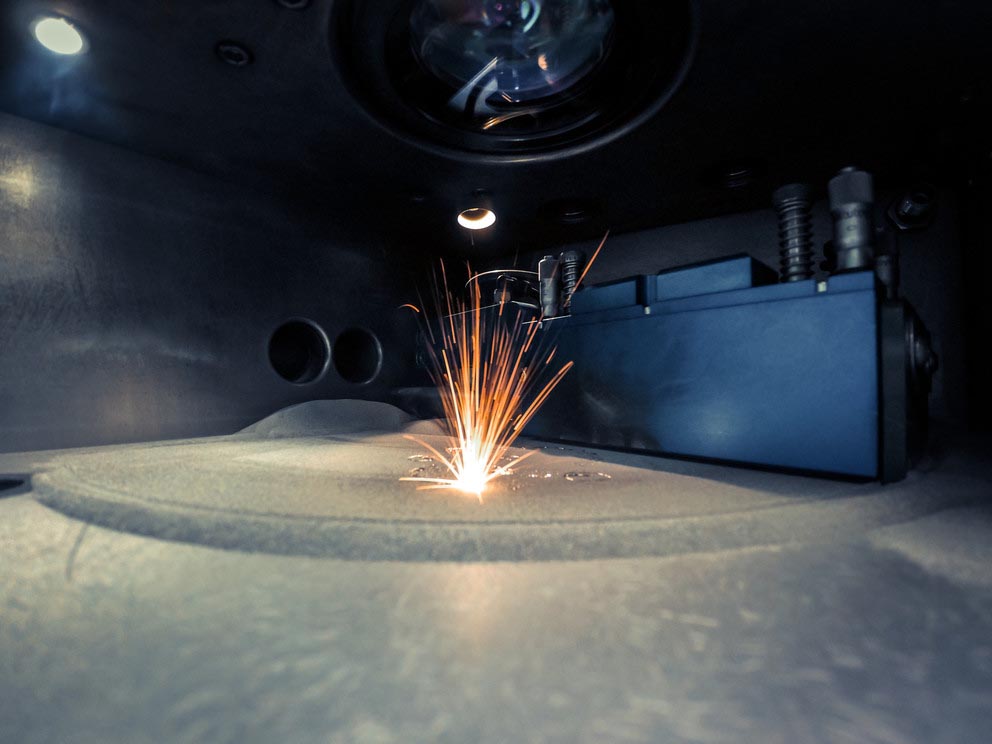
IMAGE: ISTOCK/@MARINA_SKOROPADSKAYA
Engineering researchers strive to optimize metal additive manufacturing
$546,806 grant from the National Science Foundation could enhance the models used for the technology, allowing the resulting components to be created with fewer defects
9/9/2020
By Erin Cassidy Hendrick
UNIVERSITY PARK, Pa. — In pursuit of an improved, less expensive way to additively manufacture, or 3D print, complex metal components, Penn State researchers have received $546,806 from the National Science Foundation.
The project represents the latest step forward for the Department of Mechanical Engineering’s (ME) expertise in additive manufacturing, which supports innovative programs in both research and education.
“This grant will enable a manufacturing process for high-value components with complex geometries that have many different applications,” said Qian Wang, associate head for administration in ME, professor and the principal investigator of the project.
During the three-year project, Wang aims to develop new models for laser powder bed fusion additive manufacturing (AM). This is a category of metal AM that is often used to create large and complex parts, such as those used to repair military ships. Essentially, this process deposits metal powder in thin layers and uses a laser to melt and fuse them together, repeating the process until the piece is complete.
While AM enables the creation of these parts, the process is expensive, time consuming and can often result in a flawed final component.
“You don’t want to have to use trial and error and throw them away,” Wang said. “The overall objective will be to improve the part quality and consistency, which will help increase the economic competitiveness of metal additive manufacturing.”
Currently, to avoid these problems, a widely used numerical model called finite elements is used to computationally enhance the design. However, this method is time and resource heavy, while also being difficult to adjust in real time, if needed.
Harnessing her background in dynamics and control, Wang said the new models she will develop will capture the essential physics of the process with a significantly reduced computational complexity, as compared to finite element models.
“Through this project, we are trying to find a balance between representing physics as much as possible, while not resorting to overly expensive computation,” she said.
The resulting models will be tested to improve the real-time control while manufacturing these parts, in close collaboration with Abdalla Nassar, the head of the Process Physics, Analytics and Engineering Department at the Applied Research Laboratory (ARL).
Wang and Nassar will utilize Penn State’s Center for Innovative Materials Processing Through Direct Digital Composition (CIMP-3D) for this testing. The unique facility describes itself as having unparalleled potential for advancing and deploying AM technology.
“By using CIMP-3D, we will have the ability to test the model,” Wang said. “The modeling isn’t enough. You have to demonstrate it on a real, commercial system.”