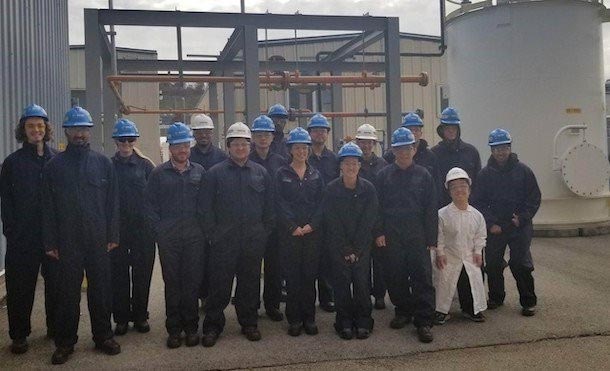
Penn State chemical engineering graduate students prepare to enter the BASF plant in Monaca, Pennsylvania, for a tour. IMAGE: CHRISTIAN PESTER
Plant visit makes chemical engineering classroom concepts come alive
2/14/2020
By Jamie Oberdick
UNIVERSITY PARK, Pa. — In the world of engineering education, even the best classroom experience cannot replace an experience in the field.
What were once concepts on a page or formulas on a whiteboard became actual experiences in a real-world setting when a group of chemical engineering graduate students visited the BASF plant in Monaca, Pennsylvania, last November.
The student field trip is organized each year by Christian Pester, assistant professor of chemical engineering and materials science and engineering, who takes graduate students from his CHE 597 Electroactive and Conductive Polymer course to the plant. The BASF plant’s focus on emulsion polymerization for the paint, construction and adhesive industries relates to class subjects such as the processing of commodity plastics used in consumer products.
“These kinds of experiences are important for the students because many of them will work in a similar plant during their career,” Pester said. “And when I was a student at the University of Bayreuth in Germany, we visited a similar industrial plant, and it was impressive to me to see something I was studying actually happening in the real world.”
The Penn State students on the BASF visit expressed the same sentiment about their experience. Nicholas Cross, a chemical engineering graduate student, was able to visualize the problems he worked on in the classroom and was astounded at the size of the operation at the plant.
“In class we do all of these problems with flow rates of thousands of pounds per hour, but you never really know what that looks like until you are at a plant,” Cross said. “The scale at which we are able to manufacture commercial chemicals and the sheer size of the equipment that is used in production never cease to amaze me.”
Chinmay Sankhe, a chemical engineering graduate student, had the opportunity to see one of his specific areas of study in action.
“I found the process control unit to be especially interesting. I have studied process control but seeing all the monitors in the process control room was fascinating,” Sankhe said. “The monitors gathered data from all the reactor units and did calculations of yield, flow rate and other quantities. These monitors could also control the safety valves. No wonder the tour guide described the unit as the heart of the plant, and someone has to be there 24/7 all year to continuously monitor the plant unit.”
Another part of the tour that impressed students was the plant’s emphasis on safety, given that engineering safety is a significant part of their education no matter their focus. The intensive monitoring of all processes at the plant was something that Michele Fromel, chemical engineering graduate student, found memorable.
“Just seeing the control room full of what seemed like endless monitors displaying the operations of all the reactors left an impression on me,” Fromel said. “It was amazing to see how much attention needs to go into each and every part of the system and how so many functions can be controlled from a remote location, separating workers from potentially harmful chemicals.”
“The trip helped remind us of the importance of safety in the lab,” Cross added. “We work with very small amounts of chemicals on our bench tops, and they work with thousands of pounds at a time. Hopefully all of the work we do eventually makes its way to a commercial process, so we need to make sure to consider all safety concerns of our scientific advancements because any safety hazards on our bench will be multiplied 1,000 times when it is commercialized.”
An added bonus of the trip was a panel presentation by BASF employees, an aspect of the visit that was especially valuable for graduate students with an eye on joining the workforce.
“A panel of BASF employees provided insight into their career paths and how they ended up where they are today,” Fromel said. “It was helpful to hear what motivated their career choices and inspiring to see how their professional lives evolved since the time they entered the workforce. It just added another benefit to an already beneficial experience.”