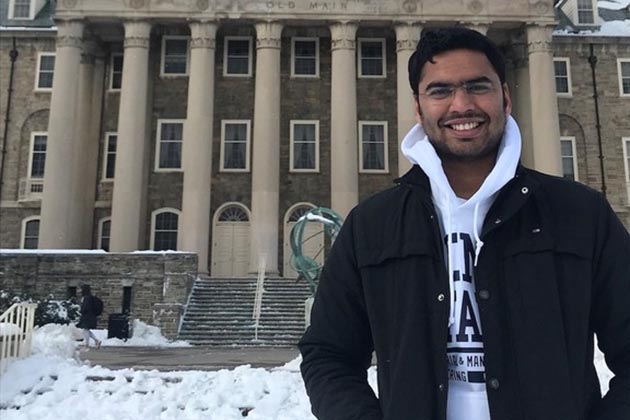
Former industrial engineering master’s student Abhijeet Golhar said the study allowed him to have hands-on experience with machines, share intellectual knowledge with others and learn more than just what is taught in the classroom. IMAGE: PROVIDED
Saving time and money via engineering: Manufacturing design
7/6/2020
By Miranda Buckheit
UNIVERSITY PARK, Pa. — A new method for machining hole patterns has implications for cost and time savings in automobile, construction and tech companies, according to a team of researchers from the Harold and Inge Marcus Department of Industrial and Manufacturing Engineering at Penn State.
One of the most notable aspects of the research was the engineers’ ability to help designers and manufacturing engineers better understand the application and production of feature patterns with sizes constrained by the location of groups of design features — geometric composite position tolerances.
The research, produced by former master’s students Abhijeet Golhar and Yiran Jiang and their advisers, El Amine Lehtihet, professor of industrial engineering, and Edward De Meter, professor of industrial engineering, was published in the Journal of Manufacturing Science and Engineering.
Currently, the American Society of Mechanical Engineers provides a universal design standard that is understandable across languages. This design standard relays the specification and interpretation of geometric tolerance design constraints, but does not specify ease or difficulty of complying with these constraints on a manufacturing shop floor.
“In manufacturing, some patterns can be difficult to produce, but traditional design specifications never tell engineers how hard it actually could be,” Lehtihet said. “The master’s students dove deep and helped us produce this study, which now provides a baseline for how difficult some of these geometric position tolerance constraints are to create on a shop floor. Sometimes companies don’t have the proper equipment to handle certain designs and have to revisit the drawing board, so this insight will save them both time and money.”
Lehtihet noted that the hard work of the former manufacturing master’s students made this study a success.
Golhar’s role in the research was to design the patterns and subsequent experiments, as well as get hands-on experience with the department’s CNC — computer numerical control — machines to manufacture the parts. The CNC machines use data to control and automate machine movements.
Mainly, the research looked at linear, rectangular and circular patterns of holes of various sizes. After Golhar created and manufactured the patterns, he had to inspect the work pieces using a Zeiss coordinate measuring machine running CALYPSO software, a common measuring tool.
The researchers used the producibility algorithm, designed for the experiment, to determine the inherent ability of the machine tool to satisfy a given pattern, subject to a composite position tolerance constraint. This analysis gave the researchers insight into how to produce particular design specifications, including indicating how difficult they are.
“The results obtained from the algorithm then needed to be analyzed to draw inferences about the patterns, such as how findings may enable designers to assess them," Golhar said. "This enables the engineers to design their manufacturing processes accordingly.”
According to Lehtihet and Golhar, this new methodology will provide a more informed approach to the specification of composite position tolerance constraints in designs.
Golhar, who graduated in May 2018, explained that the study allowed him to gain hands-on experience with machines, share intellectual knowledge with others and learn more than just what is taught in the classroom.
“Getting involved in research means a lot more learning than just studying for courses,” Golhar said. “Learning by experimentation and by the experience of your colleagues is always an add-on. You get to collaborate with others, to possibly come up with new techniques to solve the problem. Making mistakes and learning from them makes your education far more interesting.”